From a 40-story building in Singapore to a Texas highway, green concrete projects are stealthily transforming construction. Are you worried about the eco-footprint of your next construction project? Buckle up for these real-life success stories that show sustainable construction isn’t a pipe dream—it’s already a reality.
The concrete sector produces nearly 8% of the planet’s CO2 emissions, and normal concrete alone produces some 8% of global carbon dioxide output. But it’s not all green-speak correctness—innovative schemes around the world are coming up with evidence that green concrete is not simply an eco-friendly anecdote—it’s a rational, inexpensive means to mold the future of building.
Table of Contents
What Is “Green” Concrete?
Green concrete incorporates recycled materials, alternative cement products, and carbon capture technologies to dramatically reduce environmental impacts. Green concrete projects worldwide can reduce carbon emissions by 30-70% compared with traditional concrete without compromising—or even enhancing—strength.
The key ingredients that are transforming concrete are:
- Fly ash from coal-burning power plants
- Slag cement from the steel manufacturing process
- Silica fume from silicon production
- Recycled aggregates from deconstruction of buildings
- Carbon-capturing additives that bind CO2 when cured
Project 1: Microsoft’s Carbon-Negative Campus Revolution (Seattle, USA)
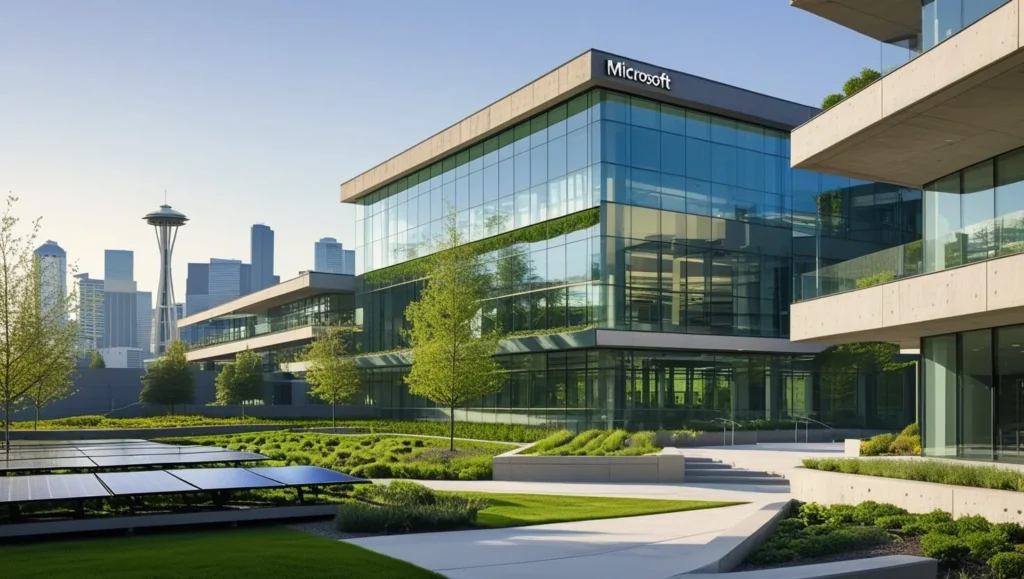
Microsoft’s carbon-negative Redmond campus shows how tech companies are leading the green building revolution. The project utilizes 30% recycled content concrete and CO2-capture technology that captures actual CO2 from the atmosphere.
Key Accomplishments:
- Carbon savings: 40% reduction in emissions over conventional concrete
- Cost-effect: Initial 15% premium offset by long-term durability benefits
- Performance: Exceeded strength targets with 12% excess
- Timeline: Construction not delayed despite introducing new material
The campus boasts 1.2 million square feet of green concrete-topped office space, parking buildings, and architectural features. Microsoft’s procurement department collaborated directly with suppliers to achieve consistent quality and supply of sustainable materials.
Lessons Learned:
Initial supplier involvement was key to the project’s success. Microsoft formed long-term relationships with concrete suppliers, allowing for a consistent flow of material and quality control during construction. This approach has become a standard practice for successful green concrete projects worldwide.
Project 2: Singapore’s Smart Nation Green Infrastructure Initiative

The government of Singapore mandated that all new public infrastructure projects use green concrete wherever technically feasible. The island-wide project has transformed how the nation builds.
Highlight Projects
- Changi Airport Terminal 5: 200,000 cubic meters of green concrete
- Marina Bay residential towers: 40-story towers with 50% recycled
- Mass Rapid Transit extensions: Underground structures using slag cement
Performance Metrics:
- Durability: 25% increase in life over normal concrete under tropical conditions
- Cost savings: 8% reduction in total project cost after economies of scale
- Environmental impact: 2.1 million tons of CO2 avoided annually
Singapore’s Building and Construction Authority now requires environmental impact statements for all major projects, with green concrete projects becoming standard practice rather than exception.
Project 3: Rio Tinto Australian Mining Plant Durability Test
Pilbara, a remote area of Western Australia, proved to be the best testing ground for green concrete durability. For seven years, Rio Tinto iron ore processing plant has operated on 100% green concrete in its harsh desert environment, making it one of the most demanding green concrete projects ever to be done.
Extreme Conditions Test:
- Temperature range: -5°C to 50°C daily fluctuations
- Corrosive conditions: Elevated salt content and mineral exposure
- Heavy machinery: 400-ton haul trucks producing constant vibration stress
Results After 7 Years:
- Structural integrity: No measurable deterioration discovered
- Maintenance costs: 35% lower than expected for ordinary concrete
- Expansion possibilities: Company now requiring green concrete for all new construction
The success of the project inspired Rio Tinto to apply green concrete specifications to their entire global operations, which inspired other mining corporations to develop similar green concrete projects.
Project 4: Denmark’s Øresund Bridge Longevity Case Study
The Øresund Bridge connecting Denmark and Sweden was partially reconstructed using green concrete to test long-term performance in marine conditions. The 16-kilometer bridge is subject to some of Europe’s harshest conditions.
Marine Environment Challenges:
- Salt water exposure: Constant spray from Baltic Sea
- Freeze-thaw cycles: Up to 50 cycles per winter
- Traffic load: 17,000 vehicles per day and intense rail traffic
5-Year Performance Review:
- Corrosion resistance: 45% better than standard concrete
- Maintenance intervals: Raised from 10 to 15 years
- Structural monitoring: Embedded sensors show stable performance
The European Union now holds up this project as a model of sustainable infrastructure, with the same specifications being used for big bridge projects all over member countries.
Project 5: Texas Highway Resilience Project
The Texas Department of Transportation tested green concrete projects on a 50-mile stretch of Interstate 35, comparing performance with traditional concrete segments under the same conditions.
Head-to-Head Comparison:
- Traffic volume: 1 120,000 vehicles per day
- Weather extremes: Between -10°C winter frosts and 45°C summer heat
- Heavy freight: 40% truck traffic with heavy loads
Three-Year Results:
- Crack resistance: 60% fewer stress cracks on green concrete segments
- Maintenance costs: $2.3 million lower than traditional segments
- Rider satisfaction: Less noise pollution and smoother surface
Texas is now mandating green concrete on all new highway construction projects, with other states testing the program with potential adoption.
Project 6: Japan’s Earthquake-Resistant Green Concrete Innovation
Japan developed earthquake-resistant green concrete to employ in reconstruction following the 2011 tsunami and earthquake. Minamisanriku city became a living laboratory for green concrete projects using this technology.
Seismic Performance Features:
- Flexibility: 30% more elastic than normal concrete
- Self-healing: Microscopic cracks self-heal with embedded minerals
- Rapid deployment: Prefabricated sections cut construction time by 40%
Disaster Recovery Success:
- School buildings: 15 buildings built in 18 months
- Residential housing: 200 homes built with green concrete foundations
- Infrastructure: Seawalls and bridges capable of surviving 500-year events
The project demonstrated that green concrete was able to outperform traditional performance in the most challenging of uses.
Project 7: Netherlands Circular Economy Demonstration
The Netherlands’ adoption of circular economy principles led to innovative green concrete projects that involved using 100% secondary materials in concrete production. Amsterdam’s Noord district was transformed into Europe’s largest circular construction site.”
Circular Materials Sources:
- Demolished buildings: 40% of aggregates from local demolition
- Industrial waste: Fly ash from nearby power plants
- Recycled steel: Reinforcement from decommissioned infrastructure
Economic Impact:
- Job creation: 300 new jobs in green concrete supply chain
- Local procurement: 90% of materials sourced within 50 kilometers
- Waste reduction: 50,000 tons of construction waste diverted from landfill
The project’s success informed EU policy, with the same circular economy requirements now being considered for major infrastructure projects across Europe.
Cost Comparison for All Projects
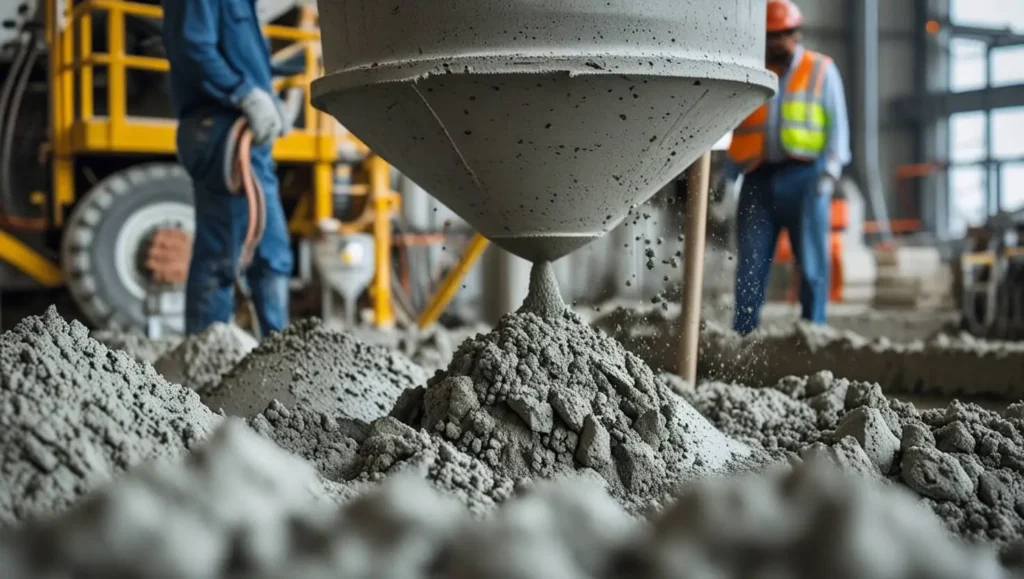
Initial Investment vs. Long-term Savings:
Upfront Premium: 5-20% higher initial costs. Break-even Point: 3-7 years, depending on project type. Total Cost of Ownership: 15-35% savings over 30-year life cycle
Key Cost Factors:
- Material costs: Decreasing as production is scaled up
- Labor training: One-time investment in a trained labor force
- Quality control: Additional testing requirements
- Maintenance: Significantly reduced long-term costs
Successful Green Concrete Projects: Key Success Factors
Such green concrete projects are successful due to many key factors that all construction managers ought to know about:
Critical Success Factors:
- Early Supplier Involvement: Develop partnerships before project start
- Quality Control Systems: Implement tough testing regimes
- Workforce Training: Invest in contractor training programs
- Performance Measurement: Use sensors and regular inspections
- Stakeholder Communication: Keep all stakeholders informed along the way
Common Pitfalls to Avoid:
- Inadequate proper testing: Proceeding without performance verification
- Supply chain mismatches: Inability to obtain stable material sources
- Specification mismatches: Improper use of incorrect green concrete type
- Maintenance neglect: Assuming “green” means means no maintenance
The Future of Green Concrete
These seven projects are just the beginning of a building revolution. The innovations currently present are:
- Carbon-absorbing concrete that can trap CO2 from the atmosphere
- Self-healing materials which automatically repair minute damage
- 3D-printed buildings with sustainable blend of concrete
- Smart concrete with embedded sensors for real-time monitoring
Frequently Asked Questions
Q: Why is green concrete more expensive than normal concrete?
A: Upfront costs are typically 5-20% higher, but lifecycle savings of 15-35% make green concrete less expensive in the long run. Most projects pay back the additional cost within 3-7 years on reduced maintenance and longer lifespan.
Q: Does green concrete perform similarly to normal concrete in extreme weather?
Yes, and often better. Green concrete projects in Australia, Texas, and Denmark show superior durability in harsh conditions, with 25-45% better performance in corrosive and temperature extremes
Q: Are construction schedules delayed with green concrete?
A: Zero delays when properly planned. Microsoft’s campus and Singapore road construction projects were on schedule. Early supplier engagement and employee training are the key things to prevent delays.
Q: What type of projects are green concrete best suited for?
A: Green concrete can be used in almost any application where conventional concrete is used, from residential to infrastructure. The seven green concrete projects demonstrate success in buildings, bridges, highways, and factories.
Conclusion
Ready to join the sustainable construction revolution? The proof is in the pudding: green concrete projects aren’t just good for the environment—they’re good for your bottom line, your building’s longevity, and your reputation as a forward-thinking builder.
The green concrete projects showcased here prove that sustainable construction has moved from experimental to essential. Whether you’re planning a small residential project or a major infrastructure development, green concrete options exist that can meet your performance requirements while dramatically reducing environmental impact. These green concrete projects demonstrate that the future of construction is both sustainable and profitable.
Take Action Today
Start your plant-based water purification journey:
- Subscribe to our Newsletter – Receive expert tips, case studies, and exclusive content on sustainable gardening and water quality solutions
Already using plants for water treatment? Share your experience in the comments below!
Related Articles
- Sustainable Technology: Building a Greener Future
- The Ultimate Guide to Polyurea Wastewater Coating for Sewage Treatment Plants [2025]
- Sustainability of Materials: 2025’s Best Innovations, Challenges, and How to Choose Wisely
- AI’s Environmental Impact: How Responsible AI Use Reduces Carbon Footprint